OVERVIEW OF TRAINING & CERTIFICATION
The School of Engineering at UBC Okanagan has launched an extensive partnership with Festo to establish a national (and Pacific Northwest) training centre for post-secondary and industrial trainings within the next 3-5 years. The aim of this partnership is to develop future employees who are well-matched to the needs of the manufacturing and mechatronics related industrial organizations, with expertise in automation, controls, and advanced manufacturing technologies. The centre is licensed by National Coalition of Certification Centers (NC3) to issue FESTO certifications.
UBC Okanagan, in partnership with the Okanagan College and industry partners, offers a non-credit Letter of Proficiency comprising 20 hours of training in the Programmable Logic Controller
(PLC) technology. The micro-credential forms part of a larger industry-endorsed certification program that is currently being implemented through the UBC Manufacturing Engineering (MANF) program. The micro-credential certificate in PLC Technology is the first micro-credential offered by the centre through funding from the Province of British Columbia, and Festo.
The certification provides the latest tools to the professional workforce in a technology that is reshaping the industry technological landscape; the training is particularly applicable to the main industry drivers of BC’s economy, including the manufacturing, forestry, oil and gas, transportation, and retail sectors.
TRAINING/CERTIFICATION OPPORTUNITIES
Skills in Industrial Automation: PLC
INDUSTRY 4.0 TOPICS
Internet of Things (IoT) – the interconnection via the Internet of computing devices embedded in everyday objects, enabling them to send and receive data.
RFID – tiny low-cost storage device(s) that are either part of the product or applied to the work piece.
Horizontal Integration – consists of companies that acquire a similar company in the same industry
Vertical Integration – consists of companies that acquire a company that operates either before or after the acquiring company in the production process.
Open Platform Communications Unified Architecture (OPC UA) – not a universal fieldbus but a software interface, which superimposes the manufacturing specific
communication and thus becomes universally accessible.
Machine-to-machine (M2M) – technology that enables networked devices to exchange information and perform actions without the manual assistance of humans.
Co-Bot / Human Robot – a robot intended to physically interact with humans in a shared workspace designed to provide worker assistance systems.
Cyber Physical Self – embedded systems when combined, form cyber-physical systems (CPS) that facilitates collaboration in networks for overlapping tasks.
Digital Twin – virtual images of the real product data that can be archived and retrieved later for evaluation.
Digital Shadow – similar to digital twin, however, not targeted on the product, but rather the value creation process and requires considerable data storage (cloud).
Big Data – extremely large data sets that may be analyzed computationally to reveal patterns, trends, and associations, especially relating to human behavior and interactions.
Supervisory Control and Data Acquisition (SCADA) – controls and monitors technical processes, couples the control devices together, and allows user friendly representation of process data using configurable and animated images.
Manufacturing Execution System (MES) – a control system for managing and monitoring work-in-process on a factory floor that has the ability to keep track of all manufacturing information in real time, receiving up-to-the-minute data from robots, machine monitors and employees.
Enterprise Resource Planning (ERP) – is the integrated management of core business processes, often in real-time and mediated by software and technology. These business activities can include: product planning, purchasing, production planning, manufacturing, or service delivery.
Smart Factory – Industry 4.0 is a name for the current trend of automation and data exchange in manufacturing technologies. It includes cyber-physical systems, the Internet of things, cloud computing and cognitive computing. Industry 4.0 creates what has been called a “smart factory”.
Smart Maintenance – based on condition monitoring where the current state of the equipment is monitored using sensors and when parameters are exceeded or performance limits are reached, error messages create outputs, that depending on automation can order parts and schedule maintenance work orders. (Predictive Maintenance)
Automation Pyramid – defines five levels of a Smart Factory (Sensors/Actuators/Hardware, PLC/PC/PID, SCADA Network, MES, & ERP)
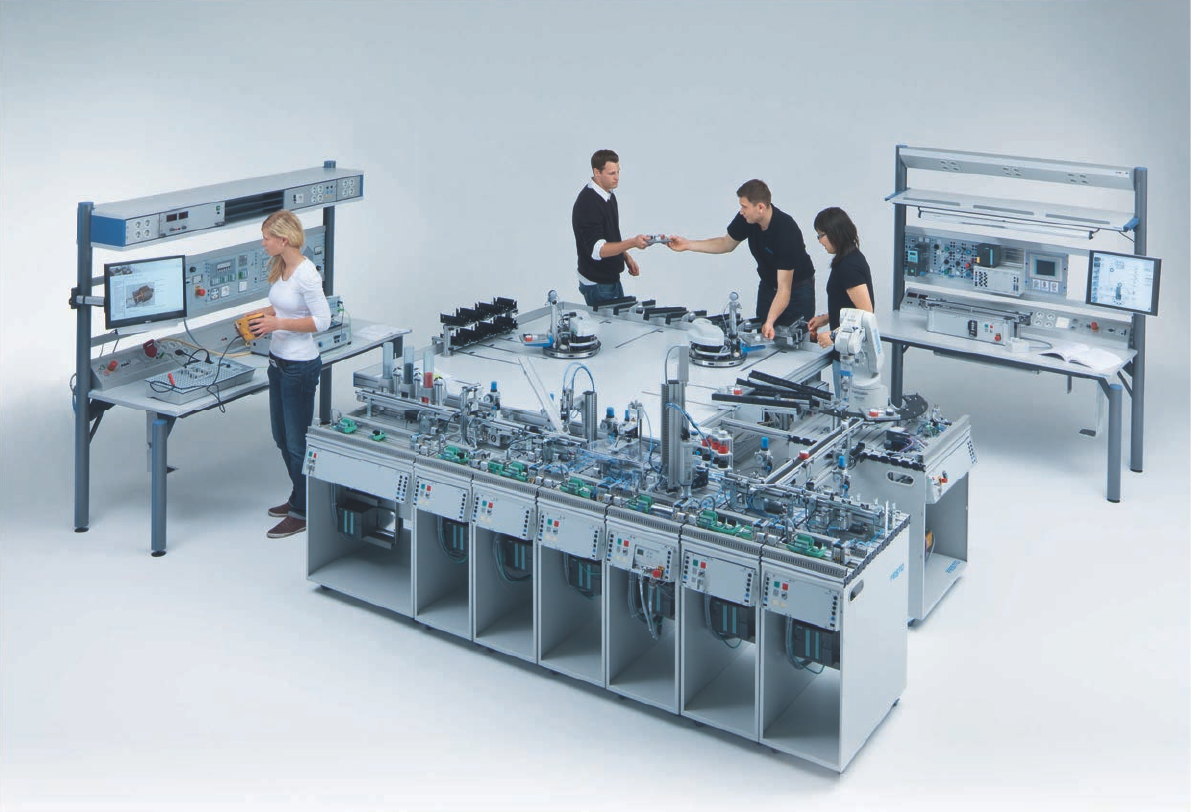
Image courtesy of FESTO learn more at festo.com